DESCRIPTION
The cylindrical plate welding machine is designed to perform the welding process without removing the bending cylinder for the butt welding process while completing the sheet metal bending process of cylindrical parts manufacturers.
Traditionally, butt welds are done manually and with column boom systems after the bending process. The sheet is placed back into the bending machine for the workpiece to reach its full cylindrical shape, and the bending process is continued. This system we have developed allows the butt welding of the cylindrical sheet without needing a second transportation process.
On the one hand, it makes it possible for you to achieve perfect and fast welding results with the deep welding method.
With the cylindrical welding machine that we have redesigned according to your company’s existing plate bending machine, it is possible to minimize labor, time, and production costs.
According to the needs, GMAW (MIG/MAG), GTAW (TIG), or Submerged Welding Machines (SAW) welding systems with oscillators can be used.
- Heating boiler
- Pressure vessel
- Fuel tanks
- Food tanks
- Expansion tannins
- Chimney production
- GMAW (MIG/MAG)
- GTAW (TIG)
- SMAW/MMA (Stick)
- Submerged Welding Machines (SAW)
FEATURES & BENEFITS
Application Examples
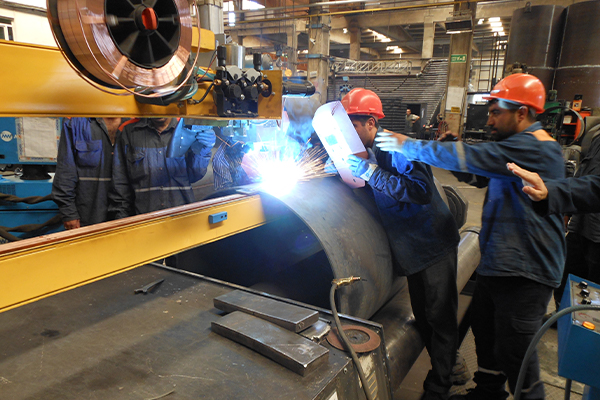
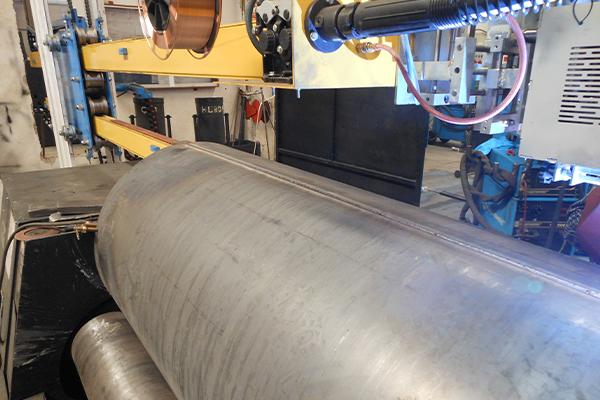
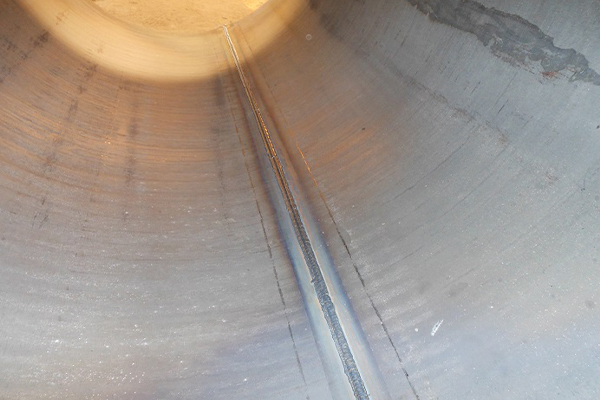
Engineered for productivity.
- Vibration-free boom movement
- Welding oscillator
- Copper backing for back welding
- Mechanical safety locks against boom drop
- Ease of adjustment and use
- Fast and high-quality weld seams
- Working with synergic power units
Standard Features
- 3-axis alignment
- Movement on linear trolley and rail
- Portable control panel
- Easy-to-use interface
- Control with the PLC system
- Pneumatic welding torch approach
- Lighting
- Water-cooled torch system (for Tig and Mig welding)
Optional Features
- Oscillator for MIG/MAG welding
- Wireless control system
- TIG or SAW power unit
- Camera inspection system
DOCUMENTS
Cylindrical Plate Welding Machine
English Brochure
Automatisches Orbitalschweißen
Deutsche Broschüre
MEDIA
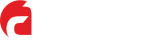
Our team of experts will help you in all situations
You tell about your production problems, we will offer solutions.
01
Tell us about your problems and your goals in manufacturing.
02
We will contact you and provide detailed negotiations.
03
Let us offer you our specially prepared solution suggestions.